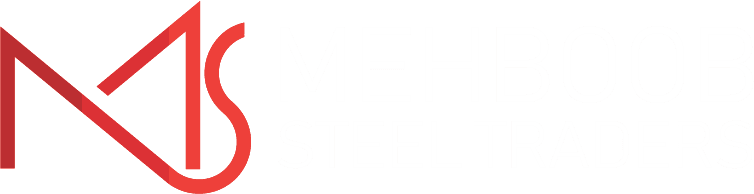
We have the best quality steel pipes. and we hope you have the best experience if you take our products
Explore
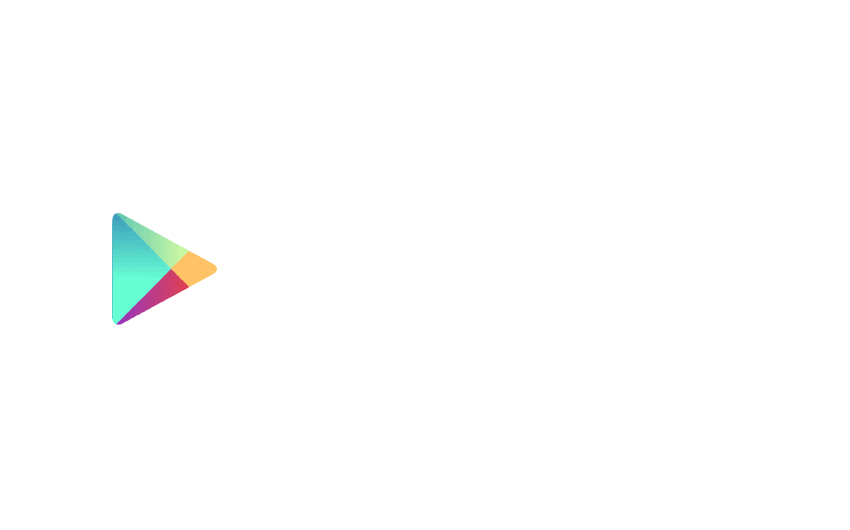
Introduction to Cold Rolled Pipes
Cold-rolled pipes are an important industrial material that passes hot-rolled steel through cold rollers at room temperature. This cold working process allows for pipes with enhanced strength, smooth surface finish, precise dimensions, and high dimensional uniformity. The cold rolling technique imparts many beneficial properties that make these pipes suitable for applications demanding precision and reliability. Let’s look deeper at the production, sizes, uses, and advantages of cold-rolled pipes.
Overview of the Cold Rolling Process
Cold-rolled pipes start as hot-rolled steel that has been annealed and descaled after initial shaping. The hot rolled steel is cooled to room temperature in the cold rolling mill and passed repeatedly between polished, unheated steel rollers.
The pressure applied by the rollers exceeds the yield strength of the steel, forcing it to plastically deform into thinner cross sections with each pass. This compressive cold working leads to up to a 40% reduction in thickness while elongating the steel.
The process is carefully controlled to achieve the stringent dimensional tolerances and surface finish requirements of cold-rolled pipes. The steel acquires its final shape of rounds, squares, or rectangles by the end.
Key Characteristics and Benefits
The main attributes of steel processed through cold rolling are increased strength and hardness, smooth surfaces, precise diameters, and uniformity along the length. Cold-rolled pipes achieve the tightest dimensional tolerances of any manufacturing process. These inherent properties make cold rolled pipes ideal for applications that demand precision machining and reliability under pressure, torque, or load.
Cold rolled pipes can be produced in a variety of standard shapes and sizes or customized to meet application requirements:
Round Pipes
Round pipes are the most common type of cold rolled pipe. They are available in outside diameters ranging from 1/2 inch to 24 inches, with wall thicknesses ranging from 0.035 inches to 0.500 inches. Their circular cross-section makes them suitable for applications involving pressure containment, transport of fluids or gases, and structural support columns.
Square Pipes
Square cold rolled pipes have 90° angled corners and equal dimensions along their width and height. Typical sizes range from 1/2 inch to 12 inches for both width and height. The main advantage of square pipes is their greater strength and stability under compressive loads compared to round pipes.
Rectangular Pipes
Rectangular pipes can be cold rolled in standard combinations of lengths and widths, such as 1 inch by 2 inches or 3 inches by 6 inches. They are typically used in structural applications as support beams, rails, and columns where higher bending strength is required in specific directions.
Oval Pipes
Cold-rolled oval pipes are produced in a range of customized dimensions as required by niche applications in certain industries. Oval cross-sections enhance strength under bending or torsional loads.
Custom Sized Pipes
In addition to standard sizes, cold-rolled pipes can be produced in custom lengths, diameters, widths, and thicknesses to meet specialized requirements. Tailored non-standard sections save material and cost.
The gauge number stamped on cold rolled pipes indicates the wall thickness of that particular size pipe. Understanding gauges helps identify the right strength pipe.
Common Gauge Sizes
The most widely used gauges for common cold rolled pipe sizes range from 24 gauge (0.0201-inch thickness) to 10 gauge (0.134-inch thickness). The popular 16 gauge has a thickness of 0.065 inches.
Thickness Range by Gauge
As the gauge number decreases, the corresponding wall thickness increases. For example, 20 gauge with a thickness of 0.0396 inches is thicker than 22 gauge at 0.0299 inches. Lower gauges represent thicker and stronger pipes.
Custom Gauges
For niche applications that require specific mechanical performance properties, custom gauges falling outside the standard range can also be cold rolled on request.
The attributes of precision tolerances, high strength, smooth surfaces, and good corrosion resistance allow cold-rolled pipes to serve varied functions across industries:
In building and construction, cold rolled pipes make durable support columns, beams, and bracing members thanks to their combination of strength and workability.
Automotive Uses
Cold-rolled steel is used to fabricate stronger, longer-lasting automotive parts including exhaust manifolds, fuel lines, and roll cages that endure vibration, heat, and collision impacts.
Mechanical Engineering Uses
The pipes are extensively used in industrial machinery to manufacture hydraulic cylinders, precision shafts, pressurized vessel parts, and other rugged components.
Furniture Industry Uses
Cold-rolled rectangular and square steel sections are frequently used in the furniture industry to make desk and table legs, racks, shelves, and steel bench frames.
Oil and Gas Uses
Thanks to their corrosion resistance, cold-rolled pipes transport crude oil, natural gas, and refined petroleum products through vast onshore and offshore pipeline networks spanning thousands of miles.
Several metallurgical advantages are driving the widespread use of cold-rolled pipes:
Improved Surface Finish
The cold rolling process achieves up to ten times smoother surface finish compared to hot rolled steel. This allows for superior paint adhesion and abrasion resistance.
Higher Dimensional Accuracy
Cold rolled pipes have the tightest dimensional tolerances to within 0.1 mm of any manufacturing process. This allows them to be precision machined for automotive and engineering uses.
Increased Strength
The cold working process makes the steel up to 20% stronger than hot rolled of the same composition, by introducing strain hardening without embrittlement.
Better Formability
Despite greater hardness, cold rolled steel retains the ductility to be safely bent, flared, and shaped extensively for applications. This formability also allows complex custom sections.
Improved Surface Hardness
The compressive forces involved increase surface hardness and wear resistance. This resists scratches and minimizes damage during handling or operation.
Reduced Risk of Distortion
The gradual controlled cold rolling process minimizes distortion defects seen in hot rolled steel that cools rapidly. Straightness and stability are assured.
While offering improved corrosion protection, cold rolled steel still requires additional coatings against rusting.
Smoother Surface Resists Corrosion
The cold rolled finish is less prone to rusting than the oxidized hot rolled surface. Defects that act as corrosive sites are eliminated.
Role of Coatings and Treatments
Further protection involves galvanizing, zinc plating, or polymer coatings that provide a physical barrier preventing surface rusting.
Susceptibility to Rusting
Despite its advantages, uncovered cold rolled steel will still eventually rust when exposed to moisture and air over months. Proper maintenance is key.
Major industrial sectors making extensive use of cold rolled pipes:
Construction Industry
Civil construction relies heavily on cold rolled pipes for bridges, buildings, marine structures, stadiums, and critical infrastructure thanks to their strength.
Automotive Industry
Automotive manufacturers use cold rolled steel for fabricating exhaust systems, fuel system components, steering columns, rear axles, and safety roll cages.
Mechanical Engineering
Cold-rolled pipes are used when building industrial machines and equipment to create hydraulic cylinders, bearing housings, shafts, press frames, and crane components.
Furniture Industry
The furniture industry relies on cold rolled rectangular and square steel sections for making bed frames, desks, racks, shelves, and bench legs thanks to the combination of strength and aesthetics.
Oil and Gas Industry
Cross-country transmission pipelines for oil and natural gas made from cold rolled steel owe their capability to withstand high pressures and harsh environments to the material’s properties.
Agricultural Equipment
Cold-rolled pipes are used when manufacturing irrigation sprinklers, agricultural tools, greenhouses, and poultry farm equipment where corrosion resistance is necessary.
Infrastructure
Urban infrastructure projects like flyovers, bridges, metro stations, and industrial plants all use cold-rolled steel components for their strength, precision, and reliability.
Summary of Key Points
In summary, cold-rolled steel pipes are formed by passing hot-rolled steel through cold rollers. This imparts precise dimensions, a smooth finish, high strength, and good ductility. Their attributes make cold rolled pipes suitable for applications in construction, automotive, oil and gas, and mechanical engineering.
When dimensional accuracy, physical strength, durability, and corrosion resistance are vital for manufacturing, construction, and industrial applications, cold-rolled steel pipes deliver immense value over hot-rolled alternatives. Their advantages justify the extra production cost.
Hot rolling forms pipes above the steel’s recrystallization temperature, while cold rolling is done at room temperature to achieve more precise dimensions, better finish, and high strength.
Construction, automotive manufacturing, industrial machinery, oil/gas pipelines, infrastructure, and furniture utilize cold-rolled pipes for their superior tolerance, hardness, and corrosion resistance.
The main reasons are cold rolling provides increased yield strength, better surface finish, precise sizing, defect-free straightness, and reduced risk of distortion during further processing.
Passing the annealed steel through cold rollers strains the pipe via compression. This strain hardening makes the steel stronger as crystalline defects are pressed out.
Galvanization, the application of a thin zinc coating, is the most common anti-corrosion treatment. The zinc acts as a sacrificial anode, protecting the steel underneath.
We have the best quality steel pipes. and we hope you have the best experience if you take our products
© 2024 Mehboob Steel Traders. All rights reserved.
WhatsApp us